5500 EX Medium Set PolyUrea/Polyaspartic
5500 EX Medium Set is a two-component aliphatic MDI polyurea-aspartic blend formulated for:
- Extended working time compared to fast-set products.
- High gloss, high-build finishes with exceptional clarity.
- Non-yellowing and UV-resistant performance.
- USDA compliance for incidental food contact.
- Available in different solid content ranges from 65%-100% solids upon customer request
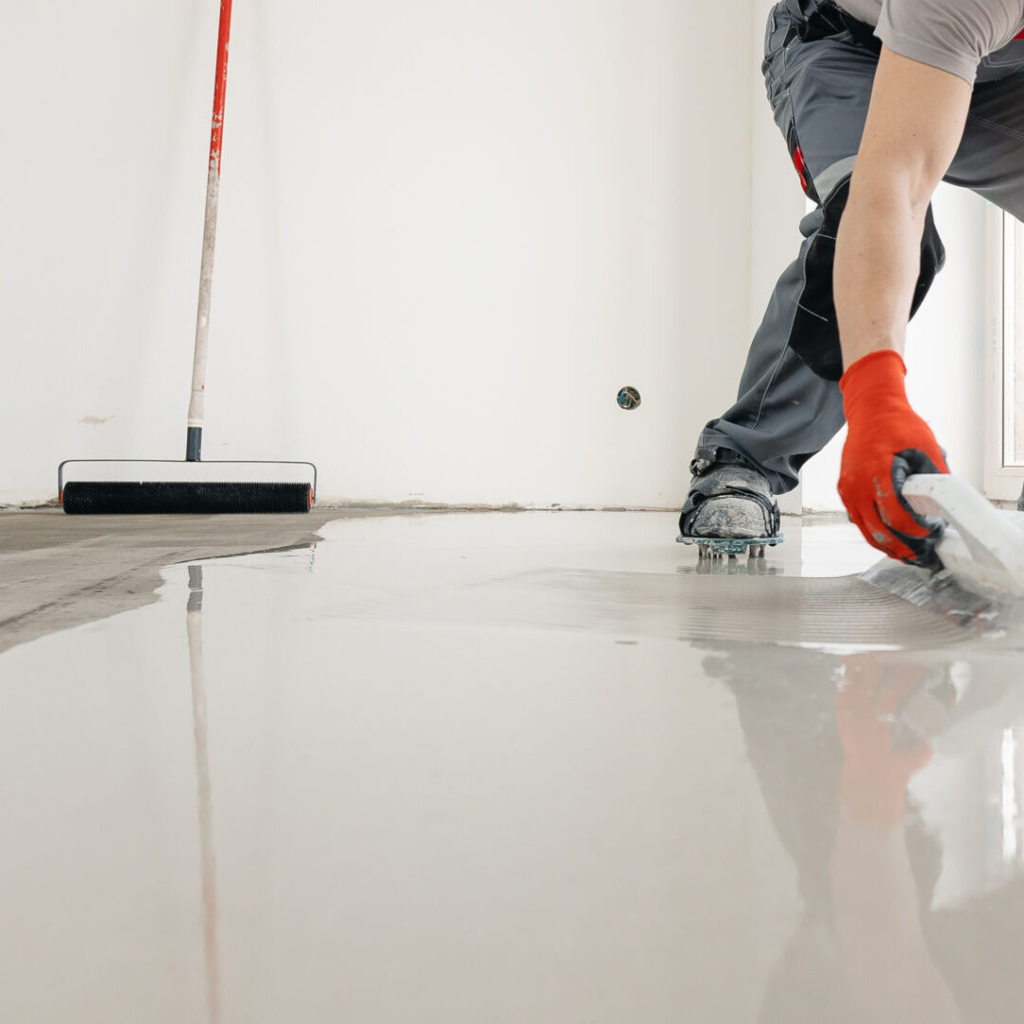
Unique Characteristics
- Ease of Use: Extended working time for easier application in larger areas.
- Customizable: Tintable with ASTC pigments and available in low-odor versions.
- Non-Skid Options: Incorporate ASTC’s “SSR” aggregate for additional safety.
- Durability: High-build protection for floors with superior elongation and flexibility.
Advantages
- UV stable and non-yellowing.
- High stain resistance, including resistance to plasticizer migration from tires.
- Excellent chemical and abrasion resistance.
- Superior adhesion to concrete and existing topcoats.
- Waterproof and elastomeric properties for robust performance.
- Quick turnaround for floor applications.
Applications
5500 EX is ideal for:
- Decorative concrete floor finishes.
- Industrial, commercial, and residential floor coatings.
- Clear topcoats for color chips and quartz.
- Kitchen floors, slabs, stairs, and pedestrian walkways.
- Exterior applications requiring UV stability.
Preparation
- Concrete Curing: Ensure a 28-day cure period.
- Surface Cleaning: Remove all contaminants, including oils, wax, and curing agents.
- Profile Creation: Abrade the surface to create a rough profile of 2-3 mils (ASTM D4259).
- Moisture Testing: Ensure moisture vapor transmission (MVT) does not exceed 3 lbs per 1,000 sq ft per 24 hours.
Priming
- Self-Priming: 5500 EX can be applied directly to concrete.
- Optional Primers: Use ASTC’s 6000 Series Epoxy Primer, 7001 Pen Prime, or 8000 CMW as needed.
Application
- Mixing:
- Combine components A and B at a 1:1 ratio using a jiffy mixer.
- Mix for 1-2 minutes without incorporating air.
- Add pigments if required, ensuring uniform dispersion.
- Coating:
- Apply with a notched squeegee and back-roll with a 1/4”-3/8” nap roller.
- Maintain a thin coat (5-10 mils) for best results.
- Recoat Timing:
- Recoat within 1-2 hours or after light sanding if exceeded.
General Physical Characteristics
Characteristic | Details |
Solids | 65%-100% |
Hardness (ASTM D2240) | Shore A 85, Shore D 50 |
Gel Time | 20 minutes at 75°F |
Elongation | 5%-6% |
Compression Strength | 24 hrs: 11,200 psi; 7 days: 14,100–19,000 psi |
UV Resistance | Excellent |
Pot Life | 25 minutes at 75°F |
Special Considerations
- Cold Conditions: Use 5500 Fast Set for applications below 50°F.
- Hot Conditions: Use 5500 HH or HHH in environments above 85°F with high humidity.
- Chemical Resistance: Resistant to a wide range of chemicals, including acids, ethanol, and motor oil.
Chemical Resistance Chart
Chemical | 24 hrs | 7 days |
10% Acetic Acid | + | Yellowing |
100% Ethanol | + | + |
Sulfuric Acid (50%) | + | + |
Motor Oil | + | + |
Brake Fluid | + | Slight Blister |
Mustard | – | Yellowing |
Limitations
- Avoid application on wet surfaces or in environments with high moisture vapor drive.
- Not all tires are tested for plasticizer staining.
- Store kits in a cool, dry environment away from sunlight.
- For professional applicators only. Refer to the MSDS before use.
Pigment Color Chart
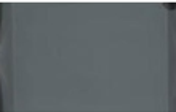
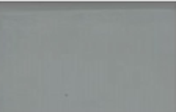
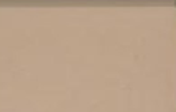
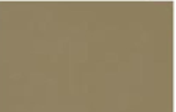
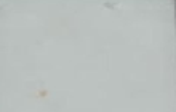
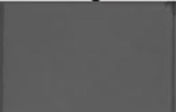
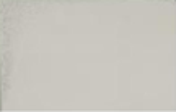
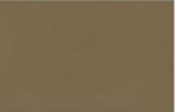
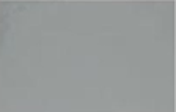
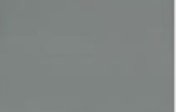
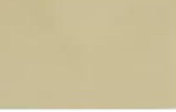
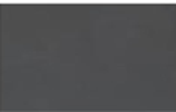
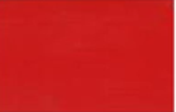
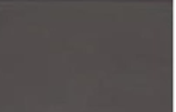
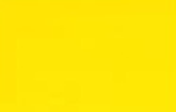
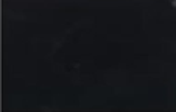
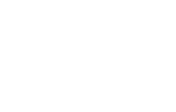