5500 HHH Extra Slow Set PolyUrea/Polyaspartic
The 5500 HHH is a two-component aliphatic polyurea/aspartic blend formulated for:
- Extra slow curing in high-heat and humid environments.
- High gloss, high build, and clear or pigmented finishes.
- Exceptional color retention, chemical resistance, and non-yellowing performance.
- USDA compliance for incidental food contact.
- Available in different solid content ranges from 65%-100% solids upon customer request
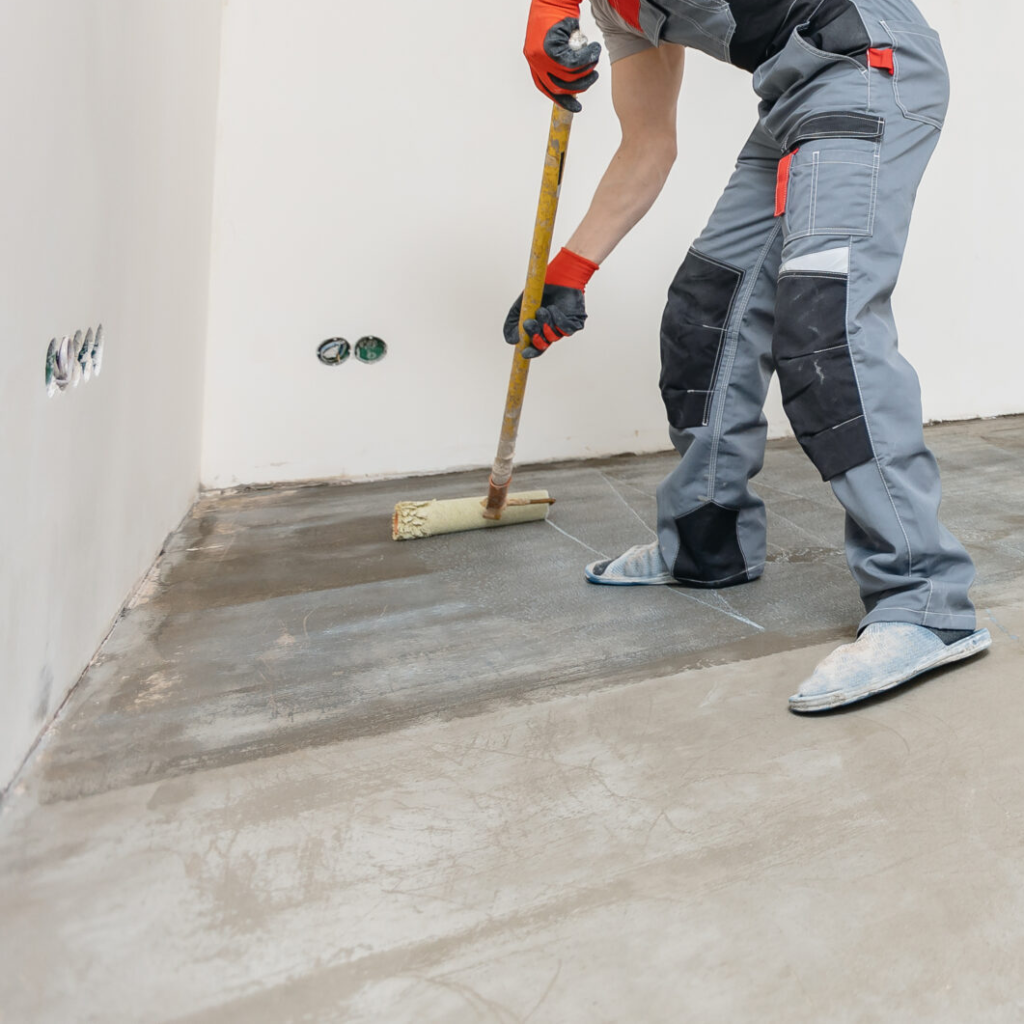
Unique Characteristics
- Extended Working Time: Ideal for areas where faster-set versions are not suitable.
- Non-Skid Options: Incorporates ASTC’s “SSR” aggregate for safety.
- Durability: High build provides added protection against wear and tear.
- Low Odor Versions: Available for sensitive environments.
Advantages
- UV stable and resistant to chalking or yellowing.
- High stain resistance to tire plasticizer migration.
- Excellent adhesion to concrete and topcoats.
- Waterproof and elastomeric properties with good elongation.
- Rapid turnaround for commercial and industrial applications.
Applications
The 5500 HHH Extra Slow Set is suitable for:
- Decorative concrete floor finishes.
- Industrial, commercial, and residential floor coatings.
- Clear topcoats for color chips and quartz.
- Kitchen floors, slabs, stairs, and pedestrian walkways.
- Exterior applications requiring UV stability.
Preparation
- Concrete Curing: Ensure a minimum 28-day cure.
- Surface Cleaning: Remove contaminants, such as oils, wax, and curing agents.
- Profile Creation: Abrade the surface to create a rough profile (2-3 mils, ASTM D4259).
- Moisture Testing: Ensure moisture vapor transmission (MVT) does not exceed 3 lbs per 1,000 sq ft per 24 hours.
Priming
- Self-Priming: Can be applied directly to concrete.
- Optional Primers: Use ASTC’s 6000 Series Epoxy Primer, 70001 Pen Prime, or 8000 CMW for enhanced performance.
Application Guidelines
- Mixing:
- Combine components A and B at a 1:1 ratio using a jiffy mixer.
- Mix for 1-2 minutes without incorporating air.
- Add pigments if required, ensuring uniform dispersion.
- Coating:
- Apply with a notched squeegee and back-roll with a 1/4”-3/8” nap roller.
- Maintain thin coats (5-10 mils) for optimal results.
- Recoat Timing:
- Recoat within 4-6 hours or after light sanding if exceeded.
General Physical Characteristics
Characteristic | Details |
Solids | 65%-100% |
Hardness (ASTM D2240) | Shore A 85, Shore D 50 |
Gel Time | 50-55 minutes at 75°F |
Elongation | 5%-6% |
Compression Strength | 24 hrs: 11,200 psi; 7 days: 14,100–19,000 psi |
UV Resistance | Excellent |
Pot Life | 25 minutes at 75°F |
Special Considerations
- Cold Conditions: Slower curing below 50°F; for faster results, use 5500 F or EX.
- Hot Conditions: Use HH or HHH versions for high-temperature, high-humidity environments.
- Chemical Resistance: Resists a wide range of chemicals, including acids, ethanol, and motor oil.
Chemical Resistance Chart
Chemical | 24 hrs | 7 days |
10% Acetic Acid | + | Yellowing |
100% Ethanol | + | + |
Sulfuric Acid (50%) | + | + |
Motor Oil | + | + |
Brake Fluid | + | Slight Blister |
Mustard | – | Yellowing |
Limitations
- Avoid application on wet surfaces or in environments with high moisture vapor drive.
- Store kits in a cool, dry environment away from sunlight.
- For professional applicators only. Refer to the MSDS before use.