6009 Primer: Slow, Fast, and Extra Fast Cure
The 6009 Primer is a 100% solids epoxy coating with:
- High durability and chemical resistance.
- Versatility in application with slow, medium, fast, and extra-fast cure options.
- A user-friendly 1:1 mix ratio.
- Resistance to amine blush and water spotting, making it ideal for challenging environments.
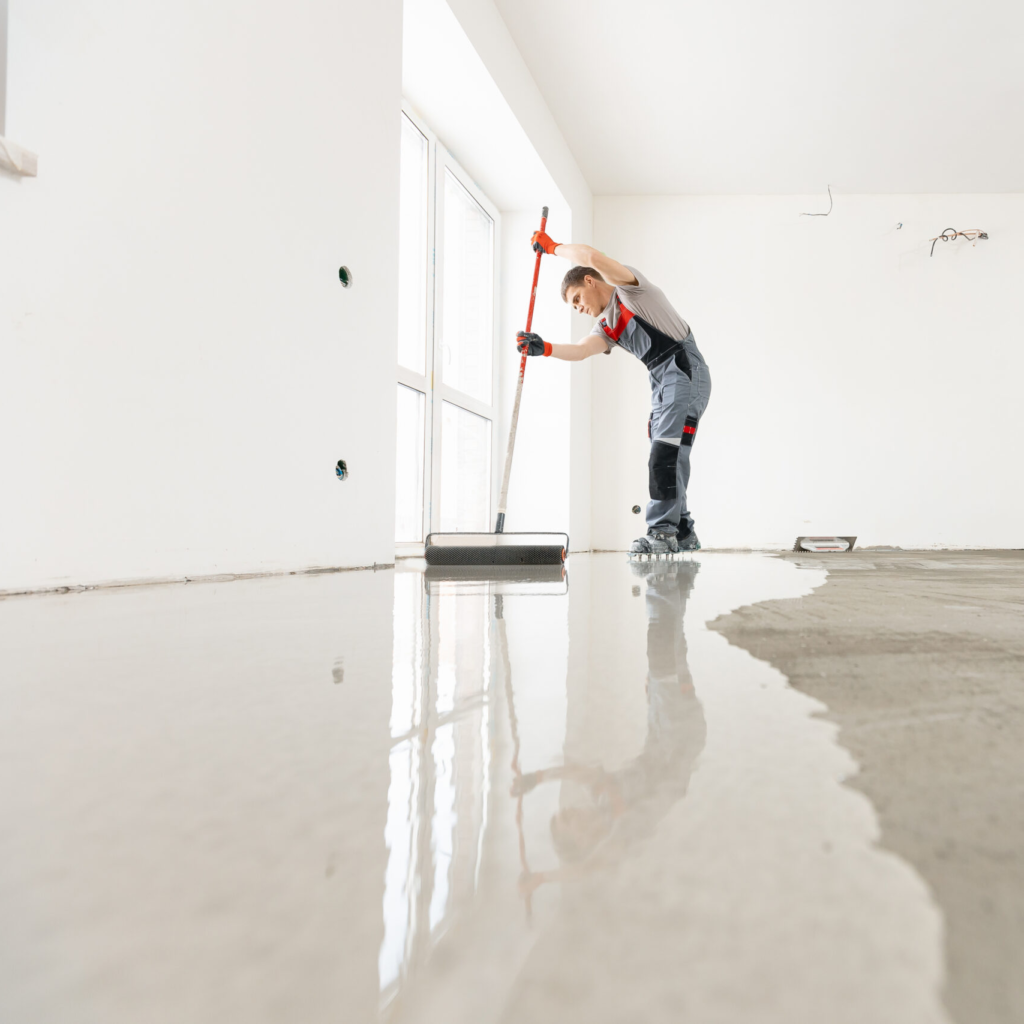
Unique Characteristics
- Strong penetration, wetting, and sealing capabilities for improved substrate adhesion.
- Durable, impact- and abrasion-resistant coating.
- Excellent hide with a single coat application.
- Designed to wick into concrete for aggressive bonding.
- Suitable for one-day installations with various cure speed options.
Advantages
- High build and excellent color stability.
- Chemical and abrasion resistance.
- Stain-resistant to most tires (plasticizer migration).
- Easy 1:1 mix ratio for precise preparation.
- No additional accelerators needed for fast installations.
- Compatible with flake and colored quartz applications.
- Supports Moisture Vapor Emissions (MVE) up to 8–10 lbs.
Applications
The 6009 Primer is suitable for:
- Decorative and solid color concrete floor finishes.
- Garage floor installations.
- Industrial, commercial, and residential flooring.
- Kitchen floors, concrete slabs, stairs, and pedestrian walkways.
- Warehouse floors and containment areas.
Preparation
- Concrete Cure: Ensure a minimum 28-day cure before application.
- Surface Cleaning: Remove contaminants, oils, wax, and old coatings.
- Moisture Testing: Conduct a moisture vapor test to ensure compatibility.
- Surface Profiling: Abrade to a rough profile of at least 2 mils.
- Crack and Void Repair: Seal and repair imperfections using ASTC-approved materials.
Priming and Moisture Vapor Reduction
- Compatible with 6000 Series Epoxy Primers, 70001 Pen Prime, and 8000 CMW.
- For higher moisture vapor transmission (up to 18 psi), use the 6007 Nova Bar Epoxy Primer.
Mixing and Application
- Mixing:
- Use a jiffy mixer with a 450 rpm drill motor.
- Mix components A and B for 2–3 minutes, avoiding air entrapment.
- Immediately transfer to a clean container and remix before application.
- Coating:
- Apply using a notched squeegee or similar tool.
- Back-roll with a short nap roller (3/8” to 1/2”).
- Maintain a film thickness of 8–10 mils per coat.
- Recoat:
- Recoat within 8–10 hours or lightly sand if exceeding the recoat window.
General Physical Characteristics
Characteristic | Details |
Solids | 100% |
Shelf Life | 1 Year |
Mix Ratio | 1:1 |
Gel Time (100 grams) | 30 minutes–1 hour |
Tensile Strength | 9,300–10,000 psi |
Adhesion to Concrete | 400–520 psi |
VOC Content | 0 g/L |
Shore D Hardness (ASTM D2240) | 72–75 |
Chemical Resistance Chart
Chemical | 24 hrs | 7 days |
10% Acetic Acid | + | Yellowing |
50% Sulfuric Acid | + | + |
Motor Oil | + | + |
Brake Fluid | + | Slight Blister |
Mustard | – | Yellowing |
Key:
- Positive Result (No Effect)
- Negative Result (Slight Effect)
Environmental Considerations
- Cold Conditions: Slower curing below 50°F; use fast-set or accelerators for improved performance.
- Hot Conditions: Faster curing above 85°F; mix smaller batches to prevent premature setting.
ASTC Color Chart
Limitations
- Avoid application on wet surfaces or standing water.
- Store product on wood pallets in a dry, room-temperature environment.
- For professional use only. Refer to the MSDS before application.
Pigment Color Chart
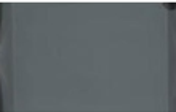
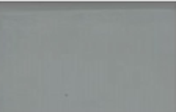
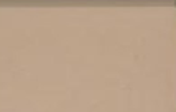
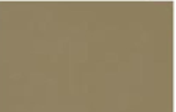
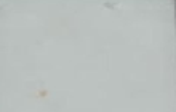
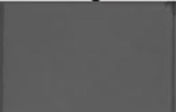
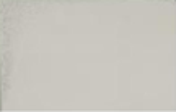
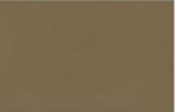
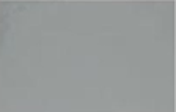
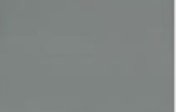
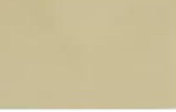
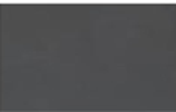
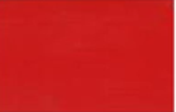
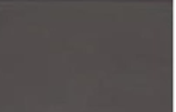
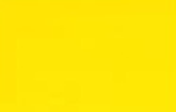
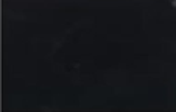
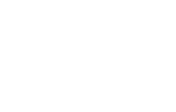