6009 W Low Viscosity Epoxy: High Performance
The 6009 W Epoxy is a 100% solids, high-build, low-viscosity epoxy coating with:
- Resistance to amine blush and water spotting.
- Enhanced durability and chemical resistance.
- Ideal for clear or pigmented finishes in industrial, commercial, and residential settings.
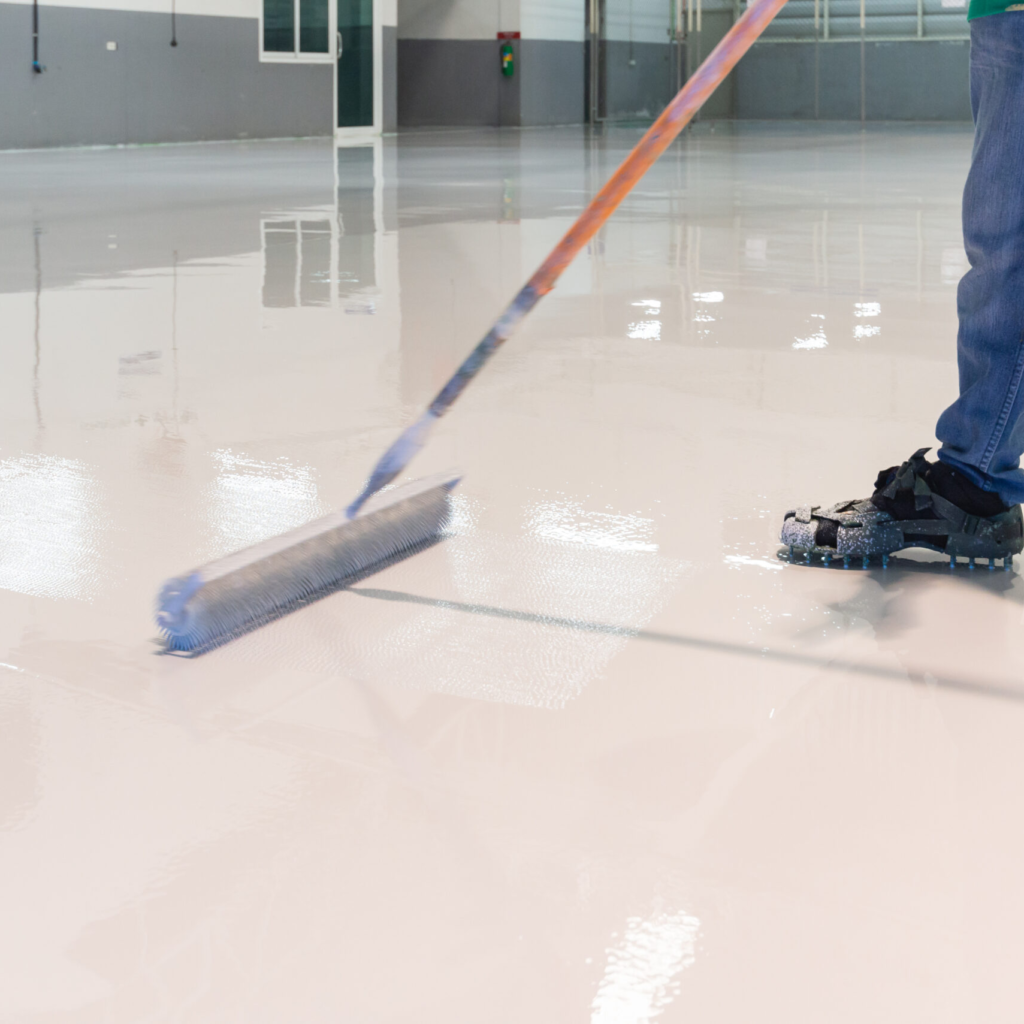
Key Features
- High Build and Clarity: Creates a glass-like, durable finish.
- Stain Resistance: Resistant to most tires (plasticizer migration).
- Chemical Resistance: Provides excellent protection against corrosive substances.
- Long Working Time: Extended pot life for easier application.
- Low Viscosity: Ensures smooth application with minimal bubbles.
- Compatible with Metallic Applications: Optimized for decorative metallic finishes.
Applications
The 6009 W Epoxy is suitable for:
- Interior Decorative Floors: Residential, commercial, and industrial environments.
- Industrial Coatings: Warehouses, containment areas, and pedestrian walkways.
- Clear or Solid Color Finishes: Suitable for color chips, quartz, and metallic designs.
Preparation
- Surface Preparation:
- Ensure a minimum 28-day concrete cure before application.
- Remove contaminants like oils, wax, and old coatings.
- Profile the surface with a minimum 2-mil roughness for better adhesion.
- Conduct a moisture vapor test to ensure compatibility.
- Priming:
- Use 6000 Series Epoxy Primers, 70001 Pen Prime, or 8000 CMW for optimal results.
Mixing and Application
- Mixing:
- Use a jiffy mixer with a 450 rpm drill motor.
- Mix components A and B in a 2:1 ratio for 2–3 minutes.
- Avoid air entrapment and immediately transfer to a clean pail for remixing.
- Pigmentation:
- Add 12–14 ounces of ASTC pigment per gallon for solid colors.
- For metallic powders, pre-mix into the B component 24 hours before use.
- Application:
- Apply with a notched squeegee and back-roll with a 3/8” nap roller.
- Maintain a film thickness of 8–16 mils per coat.
General Physical Characteristics
Characteristic | Details |
Solids | 100% |
Mix Ratio | 2:1 (A:B) |
Viscosity | 350–600 cps |
Gel Time (100g) | 3–4 hours |
Shore D Hardness | 70 |
Tensile Strength | 9,300–10,000 psi |
Flexural Strength | 94 MPa |
VOC Content | 0 g/L |
Environmental Considerations
- Cold Temperatures: Use accelerators for improved curing below 50°F.
- Hot Temperatures: Store in cool conditions to prevent premature setting in temperatures above 85°F.
Chemical Resistance Chart
Chemical | 24 hrs | 7 days |
10% Acetic Acid | + | Yellowing |
50% Sulfuric Acid | + | + |
Motor Oil | + | + |
Brake Fluid | + | Slight Blister |
Mustard | – | Yellowing |
Key:
- Positive Result (No Effect)
- Negative Result (Slight Effect)
Limitations
- Avoid application on wet surfaces or standing water.
- Store product on wood pallets at room temperature and out of direct sunlight.
- For professional use only. Refer to the MSDS before application.